Advanced Welding WPS: Customizing Requirements for Complicated Jobs
Advanced Welding WPS: Customizing Requirements for Complicated Jobs
Blog Article
Understanding Welding WPS Specifications: Best Practices and Techniques for Quality Welds
In the world of welding, grasping Welding Procedure Requirements (WPS) requirements is a crucial part that straight influences the top quality and stability of welds. Complying with these criteria makes sure consistency and integrity in welding results. However, accomplishing excellence in welds exceeds merely recognizing the standards; it involves applying finest techniques and methods that elevate the craft to a degree of precision and skill that distinguishes the average from the remarkable. As we browse with the intricacies of welding WPS requirements, discovering key insights and approaches for accomplishing top-tier welds will certainly be critical for welders looking for to master their craft and generate welds that stand the test of time.
Comprehending Welding WPS Requirements

Examiners rely on WPS paperwork to verify that welding treatments are being followed properly and that the resulting welds are of high top quality. Engineers make use of WPS requirements to make welding procedures that make sure the resilience and integrity of welded frameworks.


Important Tools for Quality Welds
Grasping welding WPS criteria is essential for welders to properly make use of the vital devices required for generating high quality welds. The kind of welding maker required depends on the welding process being made use of, such as MIG, TIG, or stick welding. Cable brushes and chipping hammers are necessary for cleaning the weld joint before and after welding to get rid of any pollutants that could impact the top quality of the weld.
Key Strategies for Welding Success
To achieve welding success, one need to master the essential strategies important for generating top quality welds. One critical technique is preserving the proper arc length. Maintaining the electrode at the ideal range from the work surface is important for producing solid, uniform welds. Additionally, managing the traveling rate is paramount. Moving as well swiftly can cause insufficient penetration, while relocating also slowly can result in excessive heat input and prospective flaws. Correct control of the electrode angle is another important technique. The angle at which the electrode is held can affect the grain form and penetration of the weld. Furthermore, making sure regular gun angle and instructions of travel is crucial for harmony in the weld bead. Last but not least, maintaining a steady hand and a stable welding position throughout the procedure is crucial to accomplishing precision and uniformity in the welds. By understanding these vital techniques, welders can elevate the high quality of their job and accomplish welding success.
Ensuring Compliance With WPS Requirements
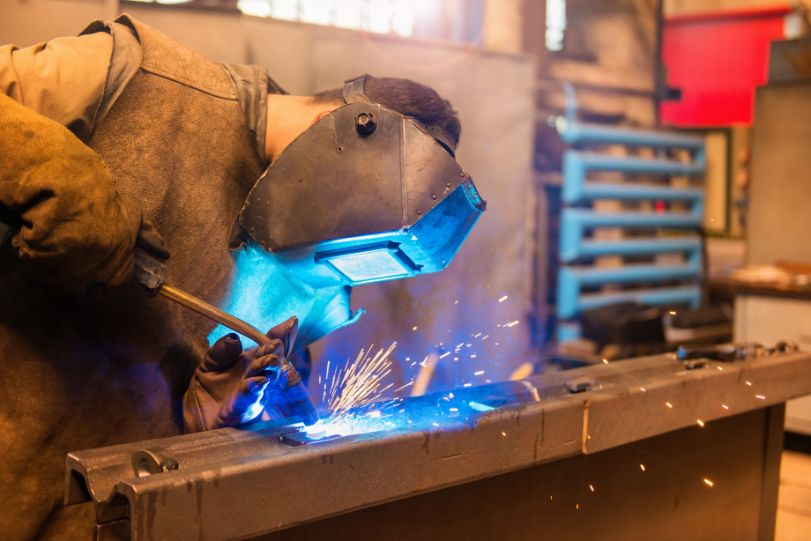
Moreover, welders ought to undertake training to familiarize themselves with the WPS criteria pertinent to their work. Regular audits and evaluations need to be performed to confirm that welding tasks line up with the recommended WPS guidelines. Furthermore, keeping detailed documents of welding criteria, equipment calibration, and evaluation results is vital for showing compliance with WPS standards - welding WPS. By diligently adhering to WPS requirements, welders can make certain that their job satisfies the necessary quality degrees and adds to the overall success of the welding job.
Troubleshooting Common Welding Issues
To resolve this, ensuring appropriate cleansing of the base steel prior to welding More Info and using the appropriate securing gas can significantly decrease porosity. Furthermore, distortion, splitting, and spatter are usual welding challenges that can be minimized through appropriate joint prep work, constant warmth control, and picking the appropriate welding consumables. By thoroughly understanding these typical welding problems and their origin triggers, welders can properly repair troubles and attain high-quality welds.
Conclusion
Finally, understanding welding WPS standards calls check over here for a complete understanding of the standards, making use of vital devices, and implementing essential techniques for successful welds. Guaranteeing compliance with WPS standards is essential for producing quality welds and preventing common welding problems. By complying with finest techniques and practices, welders can attain trusted and regular lead to their welding jobs.
In the realm of welding, mastering Welding Treatment Spec (WPS) standards is a crucial component that straight affects the top quality and honesty of welds.When delving into the world of welding methods, a vital element to comprehend is the importance and complexities of Welding Procedure Requirements (WPS) requirements. WPS standards provide a thorough standard for welding operations, making certain consistency, quality, and Homepage safety and security in the welding process. The type of welding maker needed depends on the welding procedure being utilized, such as MIG, TIG, or stick welding.Achieving welding success via the mastery of vital methods necessitates a detailed understanding and adherence to Welding Procedure Specification (WPS) requirements.
Report this page